Quality assurance of imports in focus
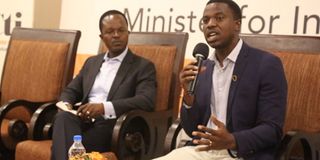
Industry and Trade minister Innocent Bashungwa speaks during a breakfast meeting with members of the Confederation of Tanzania Industry (CTI) in Dar es Salaam yesterday. Left is CTI vice chairman Paul Makanza. PHOTO | SALIM SHAO
What you need to know:
The plan was revealed by Industry and Trade minister Innocent Bashungwa during a breakfast meeting with members of the CTI
Dar es Salaam. The government is planning to undertake a study to determine the most efficient way of inspecting the quality of products imported into the country.
The plan was revealed by Industry and Trade minister Innocent Bashungwa during a breakfast meeting with members of the Confederation of Tanzania Industry (CTI) in Dar es Salaam yesterday.
He said the plan is due to government’s determination to ensure companies cut cost of doing business in the country to make Tanzania the most attractive area of investment in the Southern African Development Community (Sadc) region.
“Regulatory agencies in our ministry have been directed to work towards facilitating businesses instead of frustrating them. We will conduct a study to ascertain the best way of inspecting the quality of products,” he said.
Currently, goods are imported into Tanzania using the Pre-Shipment Verification of Conformity (PVoC) to Standards Programme. The PVoC is a conformity assessment and verification procedure applied to specific goods/products in the respective country of origin, to ensure their compliance with the applicable Tanzanian Technical Regulations and Mandatory Standards or approved equivalents.
At the breakfast meeting, CTI members said, among others, that the PVoC – which seeks to ensure quality of products, health and safety as well as protect the environment for Tanzanians – was creating delays in their businesses, proposing instead that the goods/products be verified upon reaching Tanzania (Destination inspection).
Tanzania Bureau of Standards (TBS) director general Yusuf Ngenya said: “The study will come up with the pros and cones of changing the system,” he said.
Dr Ngeya said the country used to do ‘Destination Inspection’, noting however that the same was one of the factors behind congestion of cargo at the Port of Dar es Salaam.
“In the end, when the goods were approved to be of poor quality, the importer had to ship them back to where they originated or destroy them at their own costs. The government would lose its revenue while traders would also incur extra costs in the process,” observed Dr Ngenya.
Among the issues that CTI’s first vice chairman Paul Makanza highlighted as being bottlenecks to businesses include outstanding refunds for the additional 15 per cent import duty on industrial sugar imports.
The list of complaints also includes cheap imports of PVC pipes and aluminium products along others as well as delays in issuance of work permits for expatriates and high costs of acquiring capital.
Tanga Cement financial controller Isaac Lupokela lamented over a requirement that transporters of various consignments must have receipts, obtained through an Electronic Fiscal Device (EFD) when transporting the products.
This, he argued, was in contravention of the Value Added Tax (Vat) law which requires a receipt to be issued at the end of the issuance of the transportation service.
“At that point, the actual transportation exercise has not been completed and no money has been issued for the transportation service. As such, it is impossible for the transporter to present the receipt when asked to show it to Tanzania Revenue Authority (TRA) officers at checkpoints,” he said.
In response, TRA’s Taxpayer Education director Richard Kayombo asked manufacturers to create a clear difference between goods transported by the same manufacturing firm and those transported by a transport and logistics firm.
He said the move to put checkpoints was meant to ensure that what transporters declare was exactly the same amount that was quoted in official receipts of the manufacturing firm.
“The aim is to ensure that while in certain circumstances, transporting is a completely different business from that of the one who manufactured the products, then the checkpoints give us a chance to ensure that we collect the right revenue from each of the businesses,” he said.