Prime
Why Tanzania’s textile industry is struggling
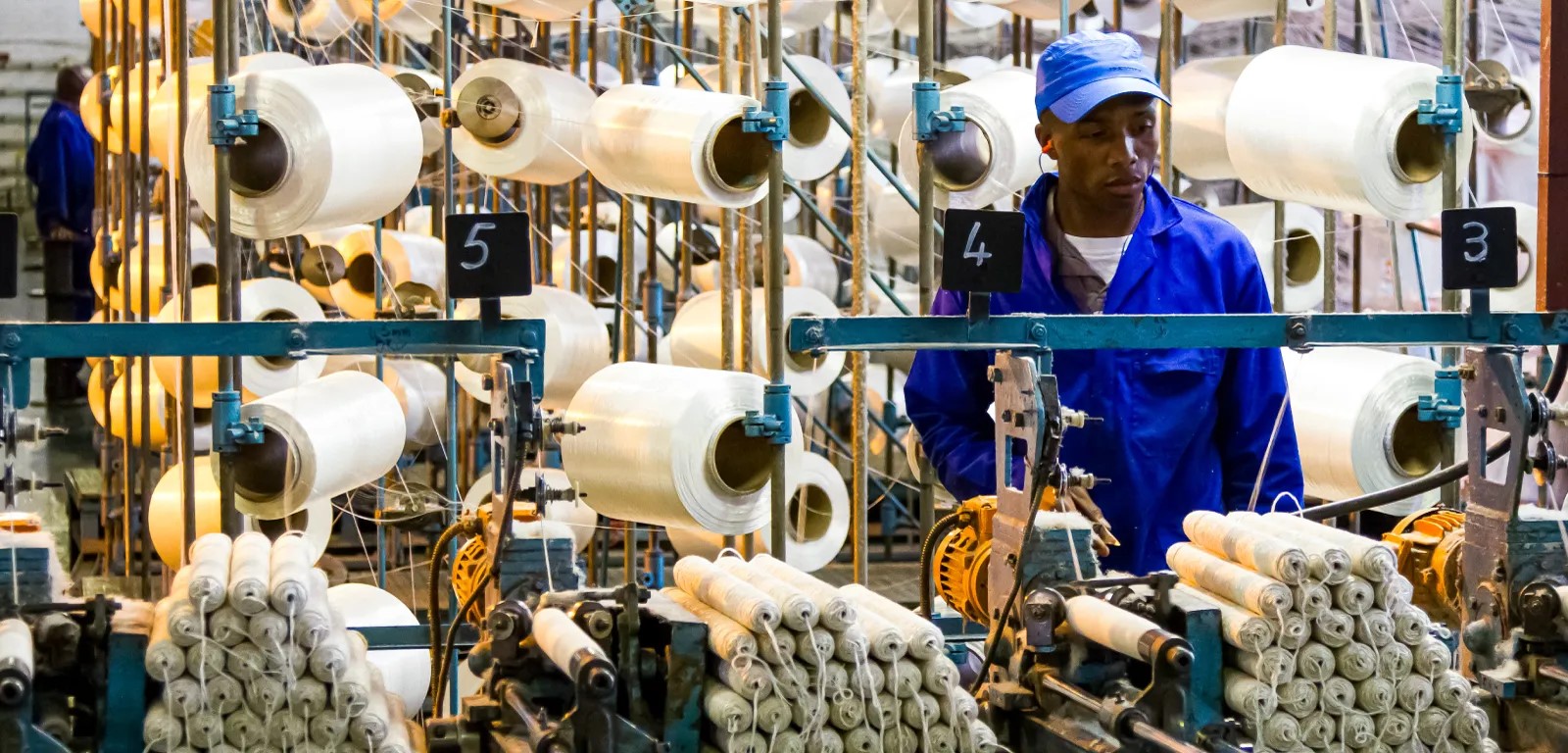
Tanzania had 33 operational textile factories in 2017, but the number has shrunk to just three currently. PHOTO | FILE
What you need to know:
- Factors include the impact of Structural Adjustment Programs and trade liberalisation policies, which opened the floodgates to cheap imports
Dar es Salaam. Once a vibrant industrial pillar, Tanzania’s textile industry is now witnessing a disheartening contraction, marked by plummeting production, factory closures and increasing investor discouragement.
From 53 million square metres of textile output in 2020 to just 32 million in 2024, the sector has shed nearly 40 percent of its production capacity in four years, according to the latest Tanzania in Figures report by the National Bureau of Statistics (NBS).
The historical context provided by Tanzania Garment and Textile Manufacturers Association (Tegamat) executive secretary Adam Zuku paints a sobering picture of a sector battered by economic reforms.
From a peak of 33 operational mills in 2017, the number has drastically shrunk to just three by 2025. Similarly, Export Processing Zone (EPZ) textile operations, once a beacon of potential, have dwindled.
Mr Zuku pointed to the detrimental impact of Structural Adjustment Programs (SAPs) by the World Bank and the IMF in the past. These programmes, alongside trade liberalisation policies, infamously known as “Ruksa”, opened the floodgates to foreign goods, including second-hand clothing (mitumba).
This influx effectively undercut local production, rendering domestic mills uncompetitive. Furthermore, the privatisation of parastatal mills, instead of leading to their revitalisation, often resulted in them being sold off, further eroding the industry.
Unfair competition
At the heart of the current crisis, according to Mr Zuku and Tegamat, is the relentless and often illicit competition from imports.
“There’s a rampant issue of tax evasion and smuggling through neighbouring countries. Goods are diverted from transit routes and dumped into our markets without paying proper duties. Some of these goods are even falsely declared by using metres instead of kilograms to lower their tax liabilities,” he said.
Compounding the problem is the “incorrect valuation” of imported goods.
Mr Zuku explained that, contrary to the EAC Customs Management Act, items like mitumba, khanga, kitenge and ready-made garments are valued by length (metres) instead of weight (kilogrammes).
“This valuation method significantly undervalues imports, reducing payable duties,” he said, adding that this gives imports an unfair price advantage.
The situation is exacerbated by a progressive reduction in effective duty rates on key textile products, making imported goods even cheaper and further eroding the competitiveness of local manufacturers.
For instance, the duty on khanga and kitenge has seen a steep decline from $1 at 50 percent in 2021/22 fiscal year to a mere $0.40 at 35 percent in the 2024/25 financial year.
“The consequence of this unchecked inflow is a market saturated with imported goods, making it impossible for local mills to compete effectively. This saturation has forced local mills to either scale back production or, more tragically, shut down entirely,” Mr Zuku said.
He also brought to light the concerning trend of direct importation by foreign agents, particularly Chinese and Indian textile factories.
These agents, often operating on temporary visas, have acquired godowns to store bulk imports and run “mali kauli” operations, characterised by a lack of proper documentation and uncertain tax payments, further enabling them to evade taxes and undercut legitimate businesses.
The cumulative effect of these challenges has been a profound investor demoralisation, as local textile investors are not only halting operations or diversifying into unrelated businesses, but some are even “actively looking for buyers for their existing textile assets”.
Mr Zuku added that some are even contemplating investing in neighbouring countries, signalling a more favourable business environment elsewhere. The sentiment among these investors is stark: No future for the textile sector if these issues persist.
Raw material hurdles and productivity pains
Beyond the import onslaught, the local textile industry grapples with fundamental issues related to raw materials and productivity.
Tanzania Chamber of Commerce, Industry and Agriculture (TCCIA) industry manager Ezekiel Kahatano told The Citizen that among primary concerns for our textile industry remains the consistent availability and quality of raw materials.
“Despite Tanzania being a significant cotton producer, factories often face shortfalls or inconsistencies in local supply that meet their specific industrial standards,” he said.
Mr Kahatano further pointed to persistent productivity gaps as a critical issue across many sectors, including textiles.
He observed a decline in output efficiency, which impacts cost-effectiveness and the ability of local industries to compete effectively both domestically and internationally.
“This productivity challenge, he notes, is not unique to textiles but is a cross-cutting issue affecting many other manufacturing industries in Tanzania.”
To address this, the TCCIA has formulated a strategic plan to strengthen domestic raw material production, particularly cotton and synthetic fibres.
“Building a more reliable supply chain is essential to reinvigorate the entire value chain,” Mr Kahatano added.
Government's stance and strategic commitments
Despite the grim assessment from industry stakeholders, the Tanzanian government affirms its commitment to reviving the textile sector.
Industry and Trade deputy minister Exaud Kigahe acknowledged the significant challenges but asserts that the government is actively taking steps to address them.
He outlined a two-pronged strategy: strengthening the cotton value chain and implementing measures to protect domestic industries.
On the protection front, Mr Kigahe said, “…we are discouraging the importation of foreign goods by increasing import costs and these strategies are ongoing.”
The government’s focus is on adding value to Tanzania’s cotton production, ensuring that the country does not merely export raw cotton but also process it into higher-value products such as fabrics and yarns.
“President Samia Suluhu Hassan’s recent visit to a cotton factory in the Simiyu Region underscored this commitment, emphasising the government’s strong resolve to elevate and add value to this vital crop, which will ultimately support and boost local textile production,” Mr Kigahe said, adding that discussions are ongoing with regard to the African Growth and Opportunity Act (Agoa) agreement.
“We are exploring avenues to extend this crucial trade pact for at least 15 years or more, recognising that textiles are among the key products benefiting significantly from this agreement.”
Agoa has proven to be a rare bright spot. According to the Ministry of Industry and Trade, Tanzania’s exports to the US under Agoa soared from $33.06 million in 2021 to $85.4 million in 2023, a 158.3 percent increase.
Tabling his docket’s 2025/2026 budget proposals in Parliament in May, Industry and Trade minister Selemani Jafo noted that textiles and apparels were among the most exported products.
Companies like Mazava Fabrics and Production EAL, Tanzania Tooku Garments Limited, Red Earth Limited and 21st Century Textiles Limited were highlighted as successfully leveraging this trade pact.
Dr Jafo also noted that the industrial sector contributed 7.3 percent to the national GDP in 2024, up from 7 percent in 2023. The sector also posted a growth rate of 4.8 percent, indicating an upward trajectory overall.
“Our focus remains on industries that add value to agricultural products and use locally available raw materials. This is key to job creation, import substitution and boosting export earnings.”
Tanzania's textile industry history is a miniature reflection of what makes domestic manufacturing difficult for many developing nations: cheap imports, weak enforcement, investment uncertainty and raw material paradoxes. Yet, the sector still holds potential, particularly if linked strategically with agriculture, export markets and regional value chains.
Since the nation is on a course towards middle-income status, it is left to choose if its destiny will be bound together by dynamic, homegrown industries, or continue to fray under the weight of unchecked global competition.
For now, the mills are growing quieter and the looms gather dust. But with coordinated action and policy resolve, the industry may still have a chance to spin a new, stronger yarn.